Feed Screeners
![[field:title/]](/uploads/211125/1-211125105R5533.jpg)
Callback
Model | DH400-DH2000 |
Capacity | 100-3300kg/h |
The discharge port can be rotated 360°, and it only takes 3-5 minutes to replace the screen.
The sieving is fine to 500 mesh or 0.028mm
Impurities and coarse materials are automatically discharged
Introduction of feed screeners
The application of feed screeners in the feed processing industry mainly focuses on two aspects: one is to clean up the impurities in the raw materials; the other is to classify the raw materials or products according to the particle size, including the cleaning of the impurities in the raw materials, the classification of crushed materials, The cleaning of impurities in the powder before granulation and the classification of granulated products.
What is the purpose of feed Screeners?
1. Grading screeners classifies feed by particle size to ensure that the feed meets the edible needs of different animals. Prevent oversized or undersized particles from affecting animal digestion and improve feed utilization.
2. Remove impurities: remove dust, fiber, metal chips, stones and other impurities in the feed to ensure the purity of the feed and prevent foreign matter from mixing into the feed, affecting animal health or clogging the equipment.
3. Improve feed quality: screen out broken, excessively powdered or substandard feed particles to improve the consistency of the finished product. Make feed particles uniform, improve palatability and promote animal growth.
4. Reduce feed waste: Reuse recyclable feed powder through screening to reduce losses, so that feed particles of different sizes can be reasonably used and avoid waste.
Applicable materials for feed screening machines
Livestock and poultry feed: pellet feed, powder feed, pellet and powder mixed feed
Aquatic feed: fish feed, shrimp feed, marine aquaculture feed
Pet food: dog food, cat food pellets, bird feed, other pet pellet feed
Agriculture and grain processing: screening of raw materials such as soybean meal, corn flour, rice bran, bran, granular or flaky food raw materials
Other industries: screening of organic fertilizers, Chinese herbal medicine powders and pellets
Benefits of feed screeners
1. The sieving is fine to 500 mesh or 0.028mm, which can satisfy the cleaning of impurities contained in different feed materials.
2. Bounce net cleaning devices are installed under the screens of each layer. By continuously hitting the screens, the materials can be screened smoothly and effectively avoid the problem of material blockage.
3. Impurities and coarse materials are automatically discharged, continuous operation is possible, and the output can reach up to 5 tons/hour
4. 1-5 layers of multi-layer screening can obtain 2-6 kinds of finished products with different specifications.
5. Fully sealed structure, no powder overflow, no liquid overflow.
6. The discharge port can be rotated 360°, and it only takes 3-5 minutes to replace the screen.
Types of feed screeners
Type |
Working principle |
Applicable materials |
Features |
Vibration screening machine |
Screening through the screen driven by a vibration motor |
Pellet feed, powder feed, premix |
High screening accuracy and efficiency, suitable for materials of different particle sizes |
Drum screening machine |
Material is graded by rotation after entering the drum |
Pellet feed, large particle material |
Simple structure, suitable for screening of large particle materials |
Plane rotary screen |
Material classification through rotary motion |
Pellet feed, pet food |
Uniform screening, suitable for high-precision screening needs |
Wind screening machine |
Separation of light and heavy materials through airflow |
Light impurities (such as bran, dust) |
Applicable to removing light impurities and improving feed purity |
Linear screening machine |
Material classification through linear vibration |
Pellet feed, powder feed |
Large processing capacity, fast screening speed, suitable for mass production |
Working principle of feed screeners
Feed screeners use a vertical motor as the excitation source, and eccentric weights are installed at the upper and lower ends of the motor to convert the rotating vibration of the motor into a horizontal, vertical, and inclined three-dimensional motion, and then transfer this motion to the screen surface. Adjusting the phase angle of the heavy hammers at the upper and lower ends can change the movement trajectory of the feed on the screen surface. The upper layer of the rotary vibrating screen can use a larger screen mesh to screen large particles or agglomerated feed. During the screening process, the exciting force generated by the vibrating motor lock is transmitted to the screen to condense into The lumps of feed are broken up for the second level of sieving.
Technical parameters of feed screeners
Model | Diameter mm | Screen area m | Screen size(mesh) | Feeding granularity mm |
DH-600 | Φ600 | 0.24 | 2-500 | <Φ10 |
DH-800 | Φ800 | 0.45 | 2-500 | <Φ15 |
DH-1000 | Φ1000 | 0.67 | 2-500 | <Φ20 |
DH-1200 | Φ1200 | 1.0 | 2-500 | <Φ30 |
DH-1500 | Φ1500 | 1.6 | 2-500 | <Φ30 |
DH-1800 | Φ1800 | 2.43 | 2-500 | <Φ30 |
DH-2000 | Φ2000 | 3.01 | 2-500 | <Φ30 |
Application of feed screeners
1. Cleaning of pellets
Feed mills are used to refer to materials that need to be crushed as pellets, including grain and meal raw materials.
Grain raw materials come directly from the field, and the impurities contained in them are relatively complex. There are two main categories: one is impurities with a larger particle size than the grain raw materials, such as stones, corn cobs, hemp flakes, straw, hemp rope, plastic flakes, etc.; the other It is soil and fine sand with a smaller particle size.
2. Cleaning of powder
The mixed feed should also be sieved with a cone primary cleaning sieve before pelleting. On the one hand, it can clean up the impurities that may be mixed in during the processing and the impurities that cannot be removed in the raw material cleaning, and on the other hand, it can break up the agglomerated materials.
3. Classification of pellet feed
In pellet feed processing, in order to increase the output of pellet mills and reduce pelletizing energy consumption, large-diameter die holes are often used for production, and then crushed into small pellets. After the particles are broken, they need to be classified to separate the too fine powder (the unformed powder in the granulation process or the powder produced in the crushing process) and the too coarse particles (the particles that are not sufficiently broken), so that they can enter The particles in the finished product processing section meet the product size requirements.
-
Used for screening, classifying and removing impurities in various powder ...
-
Granules, powders, and paddle materials can be used ...
-
What kind of vibro sifter does Feed screeners need
Feed is the general term for the food of animals raised by everyone. In a narrower sense, general fee ...
-
5 tips for selecting the most suitable vibro sifter
The vibro sifter can be suitable for screening and filtering of any particles ...
-
Common faults and solutions for vibro sifter
As the most common fine screening equipment, the vibro sifter has high screening precision ...
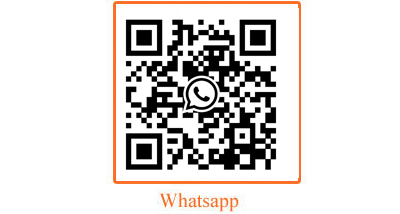
Email:
sale@xxdahan.com
WhatsApp:
+86 15236742901
Add:
1000m West of Forest Park,Yanjin County,Xinxiang City,Henan Procince,China.