Circular Sieve
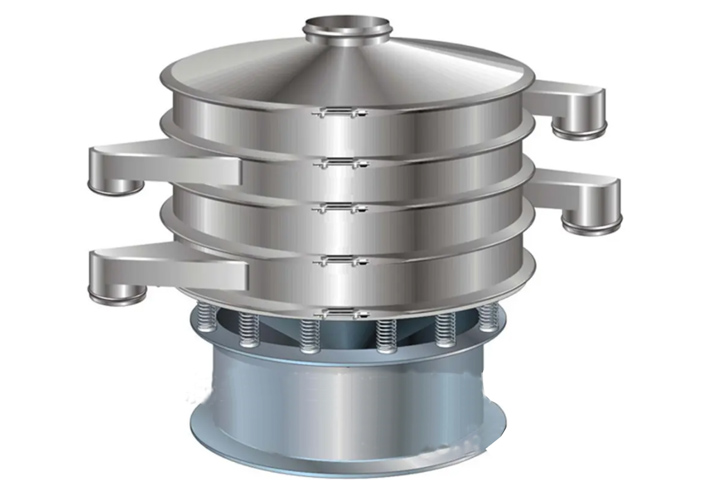
Callback
Diameter:400-600mm | Screen mesh:2-500 mesh |
Capacity:100-3300kg/h | Fast discharging, no clogging |
Accurate separation up to 5 fractions
Enclosed construction eliminates dust and fumes
The compact form requires minimal headroom to easily fit into your existing production line
Introduction of circular sieve
Circular sieve screens products by using customized layered sieve and 3D motion, it can be used to screen dry powder or granular products as well as wet products and liquids, it can eliminate foreign matter in products through continuous filtration, only 1 operation is required Up to 5 stages of product separation for precise particle size distribution. Ideal for screening incoming ingredients and final inspection of finished products, it is widely used in the food and beverage, pharmaceutical, paper and pulp, metal powder, powder coating and other industries and can be fully customized to your application.
The Circular sieve can be equipped with 1-5 sieve plates and can separate products of up to 6 sizes, standard models range in size from 400mm to 2000mm and sieve size from 51mm to 0,033mm (400 mesh), also available Different sizes and options to meet your screening needs.
Types of circular sieve
-
Vibrating Sieve
A wide range of powders can be sieved, dusted and classified, eliminating any unwanted solids and ensuring consistent and reliable handling. We can offer screening machines in a variety of single- or multi-layer configurations for batch or continuous processing.
-
Ultrasonic Vibrating Screen
Ultrasonic sieve deblinding systems have revolutionized the way intractable powders are screened on sieves. It can sieve on finer meshes (down to 20 microns) without clogging or clogging the apertures.
-
Gas Protection Vibro Sifter
Made of 304 stainless steel, gas protection hose, anti-static device, etc., it is a screening equipment for flammable and explosive materials that cannot contact air, nitrogen, etc. It adopts a fully enclosed design, and the interior can be from inert gas or Negative pressure work ensures that the properties of the product are not changed, which can effectively improve the screening accuracy and production capacity.
Working principle of circular sieve
Circular sieve uses a vertical vibration motor as the excitation source. The eccentric hammers at the upper and lower ends of the vibration motor convert the rotary motion into horizontal, vertical and inclined three-dimensional motion, and transmit it to the screen surface of the rotary vibrating screen. According to different screening requirements, the material Through 1-5 layers of screens with different mesh numbers, during this process, the cleaning devices located under the screens of each layer continuously hit the screens, so that the materials can be sieved smoothly, effectively avoiding the problem of material blockage, and materials with different mesh numbers pass through. The screens with the corresponding meshes of each layer are discharged through the outlet set at each layer to realize sieving or filtration.
Benefits of our circular sieve
1. It can be used for safe screening to remove foreign matter, separation process of solid in liquid, separation of different particle sizes in the same product, etc.
2. The screening can reach 500 mesh, providing accurate particle size, and installing a professional screen cleaning system to easily solve the problem of screen blockage.
3. The product can be classified into 6 or less parts of different sizes to achieve uniform particle size distribution.
4. Automatically process the impurities and coarse materials after screening, saving labor. After screening, it can automatically enter the next round of screening work, continuous operation.
5. Quick and easy disassembly without tools, all contact parts can be fully cleaned.
6. Noise levels are typically below 65 dBA.
Featured Video
Technical parameters
Available in the following models: 16″ (Ø 400 mm) – 24″ (Ø 600 mm) – 30″ (Ø 800 m) – 36″ (Ø 1000 mm) – 48″ (Ø 1200 mm) – 60″ (Ø 1500 mm) – 72″ (Ø 1800 mm) – 90″ (Ø 2200 mm).
Model | Diameter (mm) |
Feeding Size (mm) |
Frequency (RPM) |
Layers | Power (kw) |
Capacity (kg/h) |
DH-400 | 400 | <10 | <1500 | 1-5 | 0.18 | 100 |
DH-600 | 600 | 0.25 | 200 | |||
DH-800 | 800 | 0.55 | 500 | |||
DH-1000 | 1000 | 0.75 | 800 | |||
DH-1200 | 1200 | 1.1 | 1200 | |||
DH-1500 | 1500 | 1.5 | 1800 | |||
DH-1800 | 1800 | 2.2 | 2000 |
Dimension of circular sieve
Model | A | B | C | D | E | F | G | K | M | N | Q/2 | Full Height | ||
1 layer | 2 layers | 3 layers | ||||||||||||
DH-400 | Φ460 | Φ100 | Φ460 | 300 | 400 | 500 | 700 | Φ80 | Φ400 | 4-Φ11 | 310 | 620 | 720 | 820 |
DH-600 | Φ660 | Φ150 | Φ530 | 340 | 460 | 500 | 700 | Φ100 | Φ475 | 4-Φ11 | 400 | 620 | 720 | 820 |
DH-800 | Φ800 | Φ200 | Φ680 | 370 | 490 | 610 | 730 | Φ150 | Φ630 | 4-Φ13 | 540 | 710 | 830 | 950 |
DH-1000 | Φ960 | Φ230 | Φ800 | 420 | 540 | 660 | 780 | Φ150 | Φ750 | 4-Φ13 | 640 | 760 | 880 | 1000 |
DH-1200 | Φ1160 | Φ250 | Φ985 | 560 | 680 | 800 | 920 | Φ150 | Φ925 | 4-Φ13 | 750 | 900 | 1040 | 1180 |
DH-1500 | Φ1500 | Φ250 | Φ128 | 580 | 740 | 900 | 1060 | Φ200 | Φ1200 | 4-Φ17 | 930 | 1140 | 1330 | 1620 |
DH-1800 | Φ1800 | Φ350 | Φ190 | 1090 | 1250 | 1410 | 1570 | Φ200 | Φ1820 | 4-Φ17 | 1180 | 1504 | 1664 | 1824 |
DH-2000 | Φ2000 | Φ350 | Φ210 | 1090 | 1250 | 1410 | 1570 | Φ200 | Φ2020 | 4-Φ17 | 1360 | 1514 | 1674 | 1834 |
Circular sieve customized models and applications
Picture | ![]() |
![]() |
![]() |
![]() |
![]() |
![]() |
Application | It can filter solid and liquid or carry out size classification and impurity removal of dry material | Add ultrasonic assisted net cleaning device, which is conducive to the screening of ultra-fine and viscous materials and solves the problem of net blocking | The screen frame is increased and the feeding port is enlarged to prevent the material from splashing and easy to observe the screen. | The gate type design can prolong the screening time, improve the screening accuracy, and the material is more in and less out. | Specially designed for filtering liquids, suitable for slurries with low throughput and low impurities | Use a high-frequency vibration motor (3000 rpm) as the excitation source, suitable for filtering high-concentration slurries, such as ceramic glazes, etc. |
Three Common Cleaning Devices
When using circular sieve, many users often have the phenomenon that the sieved product clogs the screen. In this case, it is necessary to use a cleaning device. The following are three common cleaning devices:
1. Bouncing ball cleaning device: Bouncing ball is a common cleaning device. Its shape is round, and its material can be divided into two types: rubber material and silicone material. Its working principle is that it is evenly distributed on the supporting ball board, generally 5-8 are distributed within ten centimeters, and the bouncing ball will also jump and hit the screen when the screen machine is vibrating and screening, so as to clean the screen.
2. Rotary brush cleaning device: It consists of two sets of cylindrical silica gel (the number is related to the diameter of the screen frame). The rotary brush is installed in the center of the screen frame and connected by a coupling. When the screen machine is started, the rotary brush starts simultaneously, so that Clean the net at the bottom of the screen frame.
3. Ultrasonic cleaning device: This device uses an ultrasonic system to clean the screen. Its main components are composed of ultrasonic power supply, transducer and ultrasonic grid. Its principle is to convert conventional power into 18KHZ high-frequency power through the ultrasonic power supply, and act on the grid through the transducer, allowing accurate separation to 20m (#635 mesh).
Application of circular sieve
Circular sieve can sort, separate or sieve materials to the desired particle size for direct use or further processing, using vibrating motion to shake the sieve to screen out the desired product, widely used in food processing, powder handling, feed processing , pharmaceutical, chemical and other industries.
1. Removal of impurities: usually a 1-layer screen, usually fine products that pass through the screen are retained as good products, and can also be used to remove broken or undersized products. In most production environments, the inspection screen is either the first machine in the process to prevent contamination, or the last machine before the packaging machine for final quality checks.
2. Classification: Precise separation of particles of different sizes from the product so that the final material is classified into different sizes. As the particle size is very close to the aperture size, the throughput of the classifying screen is usually much slower than that of the cleaning screen, however, this can be compensated for by a larger mesh area or fine-tuning the motor weight setting.
3. Solid-liquid separation: It can quickly remove insolubles in various types of slurry. It can filter up to 100 cubic meters per hour and is suitable for the filtration of ceramic glazes, pigments, soy milk, juice and other liquids.
-
Used to safely remove contaminants and lumps in flour ...
-
Ensures removal of contaminants such as large particles and agglomerates from metal powders ...
-
Remove any contaminants in the sugar after it passes through the silo and before it is used ...
Add:
1000m West of Forest Park,Yanjin County,Xinxiang City,Henan Procince,China.