Pharmaceutical excipient powder vibrating screen
Pharmaceutical excipient powder vibrating screen is a screening device designed to meet the special physical and chemical properties of pharmaceutical excipient powder (particle size 10-500μm, mesh size 20-500 mesh), strict mesh size (particle size) classification requirements and pharmaceutical production requirements. Its core function is to achieve particle size separation and classification, impurity removal and quality control of pharmaceutical excipient powder through mechanical vibration to ensure uniform particle size of excipients. The equipment is optimized and designed based on the characteristics of pharmaceutical excipients in terms of particle size distribution, fluidity, hygroscopicity, etc., and has the characteristics of high precision, high cleanliness and good sealing.
Applicable materials for pharmaceutical excipient powder vibrating screen
Pharmaceutical excipients usually include lactose, starch, microcrystalline cellulose, talc, silicon dioxide, etc., and their particle size range is mostly between 40 mesh (about 425μm) and 400 mesh (about 38μm). Different application scenarios (such as tablets, granules, capsule filling, etc.) correspond to different screen meshes. Pharmaceutical excipient powder vibrating screens need to be able to adapt to a variety of needs from coarse screens (such as 60 mesh) to ultrafine screens (above 300 mesh).
What is the main function of the pharmaceutical excipient powder vibrating screen?
The main functions of the pharmaceutical excipient powder vibrating screen can be summarized as follows. The core goal is to improve the quality of drugs and ensure production safety:
Screening and impurity removal: Through high-precision screens, large particles, lumps, foreign matter or fibers in pharmaceutical excipients are removed to ensure the purity of excipients and avoid affecting the quality or process of drugs.
Particle size classification: According to different sieve mesh numbers, the excipients are graded to obtain powders with uniform particle size distribution, which improves the process performance and consistency of the excipients in subsequent mixing, tableting, filling, granulation and other processes.
Improve fluidity and uniformity: The powder after screening by the pharmaceutical excipient powder vibrating screen has better fluidity, and the particle size difference between particles is reduced, which helps to mix evenly and reduce the risk of deviation. It is particularly suitable for the uniform distribution requirements in solid preparations.
Pretreatment and guarantee of tableting quality: Screening of excipients before tableting helps prevent problems such as die blocking, uneven tablet weight, abnormal disintegration, etc., and improves tableting stability and yield.
What are the advantages of pharmaceutical excipient powder vibrating screens?
Solve the problem of stickiness and agglomeration: Many excipients, especially fine powders or excipients with certain chemical structures, show obvious inter-particle attraction, resulting in agglomeration, aggregation and adhesion to the screen. This reduces throughput and efficiency. By applying high-frequency vibration to the screen, fine, sticky powders are prevented from adhering and blocking the aperture.
Dealing with the hygroscopicity of pharmaceutical excipients:Some excipients easily absorb moisture from the environment, causing them to become sticky, agglomerate and block the screen holes. The closed design and smooth, non-porous materials minimize the exposure of pharmaceutical excipient powders to moisture during the screening process and reduce moisture retention on the surface of the equipment.
Dealing with irregular particle shapes:Excipients with irregular or elongated particle shapes orient themselves and get stuck in the screen, causing blockage and reducing efficiency. The vibration frequency and amplitude of the pharmaceutical excipient powder vibrating screen can be adjusted, or the slope and discharge angle of the hopper can be adjusted to promote gravity flow and reduce material retention.
Dealing with the fragility of pharmaceutical excipient powders:Some excipients are brittle and may break down or produce fine powder during vigorous sieving, which may change their particle size distribution and affect the quality of the final product. By controlling the vibration intensity, the shear force on fine particles can be reduced to prevent excessive wear of fragile materials.
Recommended mesh number of pharmaceutical excipient powder vibrating screen
The recommended mesh number of pharmaceutical excipient powder vibrating screens should be selected according to the physical properties of different excipients, usage scenarios (such as tableting, capsule filling, coating, etc.) and specific requirements for particle size distribution.
Name of pharmaceutical excipients |
Recommended mesh size |
Description |
Lactose |
60-200 mesh |
Commonly used for tablet/capsule filling, to remove agglomerates or coarse particles |
Microcrystalline cellulose |
60-120 mesh |
Controls fluidity and tableting performance, removes fiber agglomerates |
Corn starch |
80-200 mesh |
Commonly used as excipient, binder or disintegrant, requires uniform particle size |
Talc |
200-325 mesh |
Extra fine powder, commonly used for coating, requires high fineness and cleanliness |
Sodium carboxymethyl starch |
100-200 mesh |
Used for disintegrant, uniform fineness Helps tablet dispersibility |
Hydroxypropyl methylcellulose |
80~200 mesh |
Used as tablet sustained-release and controlled-release coating, particle size affects dissolution rate |
Silicon dioxide |
200~400 mesh |
Used in very small amounts but requires high fineness, ultrasonic vibrating screen is recommended for ultrafine screening |
Application of pharmaceutical excipient powder vibrating screen
Pharmaceutical excipient powder vibrating screen is mainly used for particle size classification, impurity removal and quality control in the production process of different dosage forms (such as tablets, capsules, granules), ensuring that the particle size of the excipient powder is uniform, pure and free of impurities, so as to meet the requirements of each dosage form process for the physical properties of the excipient.
Tablet production process: Control the particle size of the excipient to ensure that it has good fluidity and compressibility, and remove coarse particles or foreign matter that may affect the appearance and stability of the tablet. Match the particle size of different excipients before mixing to avoid stratification and ensure uniform mixing of drug ingredients and excipients.
Capsule production process: Ensure that the capsule filler has good fluidity, thereby ensuring uniform filling and dosage accuracy of the capsule, and remove clogging coarse particles or foreign matter. The pharmaceutical excipient powder vibrating screen can accurately screen excipients that require a specific particle size, such as lactose as a diluent or silicon dioxide as a glidant.
Granule production process: Control the particle size of the excipient to ensure that it is evenly mixed with other ingredients. Preliminary screening of wet granules after granulation to obtain a roughly uniform particle size, providing a basis for subsequent drying and granulation. After drying and granulation, the dry granules are finely screened to remove over-fine powder and over-coarse particles.
Pharmaceutical excipient powder vibrating screen is a key equipment in the pharmaceutical process. Its design must take into account particle size control accuracy, hygiene standards and operational flexibility. Through high-frequency vibration, multi-layer screens and anti-static technology, the particle size consistency and quality stability of the excipient powder are ensured.
-
Potato Starch Vibrating Screen
Granules, powders, and paddle materials can be used.
-
Screening black soldier fly feces and larvae can separate the worms and feces, saving labor.
-
Ensures removal of contaminants such as large particles and agglomerates from metal powders, providing accurate particle size distribution
-
Remove solids from liquid slurries and recover valuable materials in the waste stream for reuse.
-
Desert sand sieving machine
Desert sand sieving machine is a mechanical equipment used for sand and gravel processing or sieving...
-
Powder Vibrating Screen
As an efficient screening equipment, powder Vibrating Screen plays an important role in industrial...
-
Powder Vibrating Screen
As an efficient screening equipment, powder Vibrating Screen plays an important role in industrial...
-
Centrifugal screening machine
Centrifugal screening machine is designed and produced for screening problems such as light materials...
-
Vibrating screen for coal gangue screening
Z-type bucket elevator for peanut conveying is a vertical lifting equipment specially designed for fragile or soft conveying...
-
100 mesh vibrating slip screen
100-mesh vibrating slip screen can effectively separate fine particles with a particle size of less than 0.15 mm from coarse...
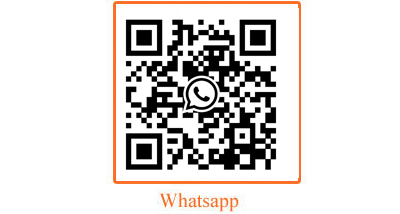
Email:
sale@xxdahan.com
WhatsApp:
+86 15236742901
Add:
1000m West of Forest Park,Yanjin County,Xinxiang City,Henan Procince,China.